NDT
OVERVIEW
Rock Marine Services offers a wide range of Non-Destructive Testing (NDT) services to evaluate the properties of materials, components, and systems without causing damage. Our goal is to determine the integrity and reliability of structures and components and to identify any defects or anomalies that could compromise performance or safety. Our NDT services include various methods such as visual inspection, radiography, ultrasonics, magnetic particle inspection, liquid penetrant inspection, and eddy current testing. Each method has its own set of advantages and limitations. Our NDT services are commonly used in industries such as aerospace, oil and gas, construction, and manufacturing to ensure the safety and integrity of equipment and structures. Our certified and qualified personnel perform these services and the results of the testing are usually documented in a report that includes a detailed description of the method used, the results of the testing, and any defects or anomalies that were identified.
- Visual inspection: This is the simplest and most basic form of NDT, and involves looking at the surface of a material or component with the naked eye or with the aid of a magnifying glass, microscope, or borescope. Visual inspection is often used to detect surface defects such as cracks, corrosion, and surface finish issues.
- Radiography: This method uses X-rays or gamma rays to create an image of the internal structure of a material or component. Radiography can be used to detect internal defects such as cracks, voids, and inclusions that are not visible on the surface.
- Ultrasonics: This method uses high-frequency sound waves to create an image of the internal structure of a material or component. Ultrasonics can be used to detect internal defects such as cracks, voids, and inclusions that are not visible on the surface.
- Magnetic particle inspection: This method uses a magnetic field to detect surface or subsurface defects in ferromagnetic materials. Magnetic particle inspection is often used to detect cracks, laps, seams, and other surface discontinuities.
- Liquid Penetrant Inspection (LPI): This method uses a liquid penetrant that is applied to the surface of a material or component and then removed. Any defects on the surface will allow the liquid to penetrate, and the excess liquid will be visible and indicate a defect.
- Eddy Current Testing (ECT): This method uses electromagnetic induction to detect surface and subsurface defects in non-ferromagnetic materials. Eddy current testing is often used to detect cracks, laps, seams, and other surface discontinuities.
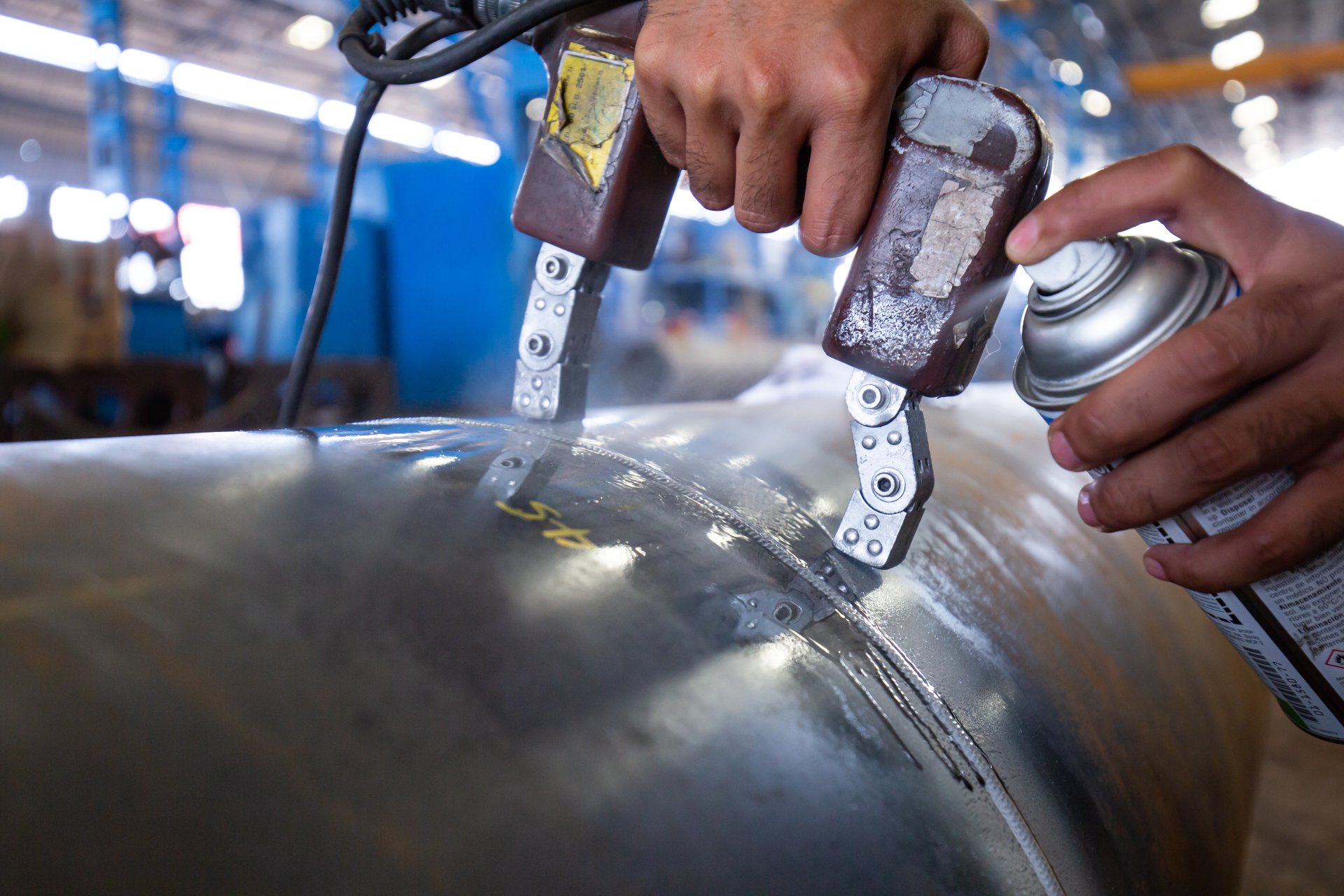